Unraveling the Importance of Injection Mold Tool in Modern Manufacturing
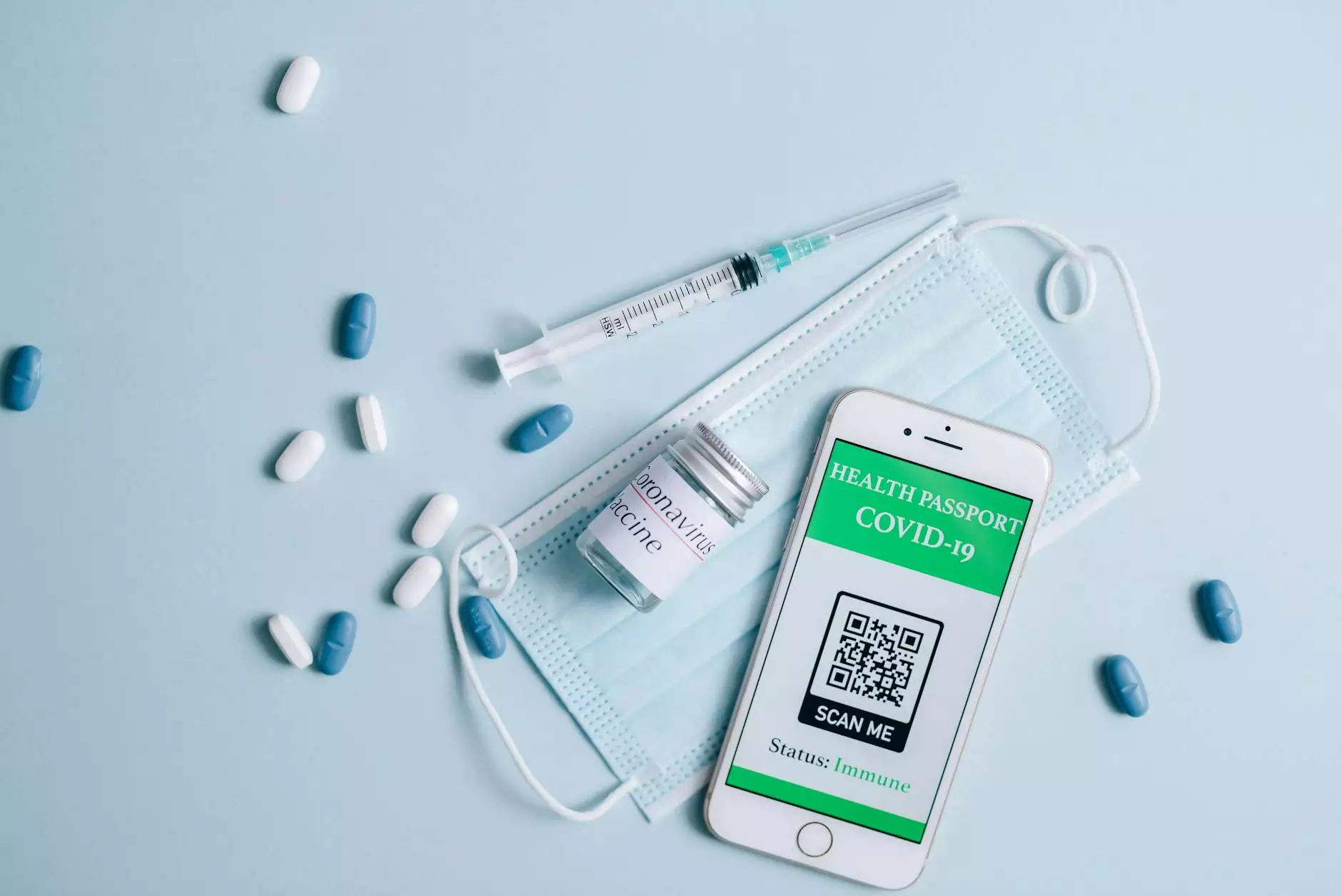
In today's fast-paced and dynamic manufacturing landscape, businesses are constantly looking for methods to enhance productivity while maintaining the highest standards of quality. One of the most pivotal elements in this area is the injection mold tool. This article delves deep into the significance of injection mold tools, their functionalities, and how they contribute to the overall efficiency of the manufacturing process.
What is an Injection Mold Tool?
An injection mold tool is a specialized device used to create plastic products through the process of injection molding. This technique involves injecting molten plastic into a mold cavity, where it cools and solidifies into the desired shape. The design and precision of the injection mold tool directly affect the quality of the final product.
Key Components of an Injection Mold Tool
An injection mold tool comprises various essential components that work in harmony to produce high-quality plastic parts. These components include:
- Mold Base: The foundational structure that holds the other components and provides stability.
- Cavities and Cores: Forms that define the shape of the finished product. Cavities are the hollow spaces where the material fills, while cores create internal features.
- Ejector Pins: Mechanisms that remove the finished part from the mold once it has cooled and solidified.
- Cooling Channels: Pathways within the mold that circulate coolant to maintain optimal temperatures for efficient production.
- Ventilation Systems: Ensures that gases escape during the molding process to prevent defects in the final product.
The Process of Injection Molding
Understanding how an injection mold tool works is crucial in appreciating its role in manufacturing. The injection molding process can be divided into several key stages:
1. Material Preparation
The process begins with the preparation of the raw plastic material, typically pellets. The pellets are fed into a hopper, where they are heated until they melt into a viscous state.
2. Injection Phase
Once the plastic reaches the desired temperature, it’s injected into the mold at high pressure. This injection phase is critical, as the speed and pressure can significantly influence the quality of the final product.
3. Cooling Phase
After injection, the molten plastic is allowed to cool. This cooling phase solidifies the plastic and gives it its final shape. Cooling can take anywhere from seconds to minutes, depending on the mold design and plastic material used.
4. Ejection Phase
Once the part is adequately cooled, the mold opens, and ejector pins remove the part from the mold cavity. This phase must be executed with precision to avoid damaging the finished product.
Advantages of Using Injection Mold Tools
Injection mold tools offer numerous advantages, making them a preferred choice in the manufacturing industry:
- High Production Rates: Injection molding allows for rapid and efficient production of large quantities of parts, significantly reducing production time.
- Cost-Effectiveness: Although the initial cost of creating a mold can be high, the long-term benefits and efficiencies lead to lower per-unit costs.
- Design Flexibility: Injection mold tools can produce complex shapes and designs that would be challenging or impossible with other manufacturing methods.
- Consistent Quality: The process ensures high levels of consistency and precision in the production of plastic parts, critical for quality control.
- Reduce Waste: The injection molding process minimizes material waste due to its efficiency and the ability to reuse scrap materials in some cases.
Choosing the Right Injection Mold Tool
When it comes to selecting an injection mold tool, several factors should be considered to ensure optimal performance. These include:
1. Material Compatibility
Your chosen mold tool must be compatible with the materials you intend to use. Different plastics have varying optical and thermal properties that might influence the mold design.
2. Mold Design
The design of the mold should align with the complexity and requirements of the final product. This includes considerations for draft angles, wall thickness, and spacers for multi-cavity molds.
3. Precision and Tolerance
High precision and proper tolerances are crucial for ensuring that the final product meets specifications and fits correctly in its intended function.
4. Supplier Reputation
Working with a reputable supplier, like DeepMould.net, can greatly influence the quality and reliability of your injection mold tool. Ensure that the supplier has a proven track record in the industry.
DeepMould.net: Your Partner for Quality Injection Mold Tools
At DeepMould.net, we specialize in providing high-quality injection mold tools tailored to meet the specific needs of various industries. Our expertise in metal fabrication and advanced injection molding techniques allows us to deliver precision-engineered solutions that stand out in the market.
Why Choose DeepMould.net?
- Expertise: Our team of seasoned professionals brings years of experience in the manufacturing sector, ensuring that you receive the best advice and solutions.
- Quality Assurance: We adhere to stringent quality control measures to guarantee that our injection mold tools meet the highest industry standards.
- Cutting-Edge Technology: Utilizing the latest in manufacturing technology, we provide innovative solutions that improve production rates and product quality.
- Customization: We understand that every project is unique. Our injection mold tools can be fully customized to fit your specific requirements.
- Robust Customer Support: Our commitment to customer satisfaction means we work closely with you through every step of the process, from design to delivery.
Conclusion
In conclusion, the injection mold tool is essential in today’s manufacturing world, providing efficiency, quality, and cost-effectiveness. With the ability to create complex designs and maintain consistent quality, injection molding stands as a cornerstone of modern production methods. Companies like DeepMould.net exemplify the advantages of using high-quality injection mold tools, ensuring that businesses can meet their manufacturing goals effectively. Investing in the right mold tool can elevate your production capabilities, boost your profitability, and keep you competitive in the ever-evolving market.