Revolutionizing Automotive Manufacturing: The Role of Injection Molding
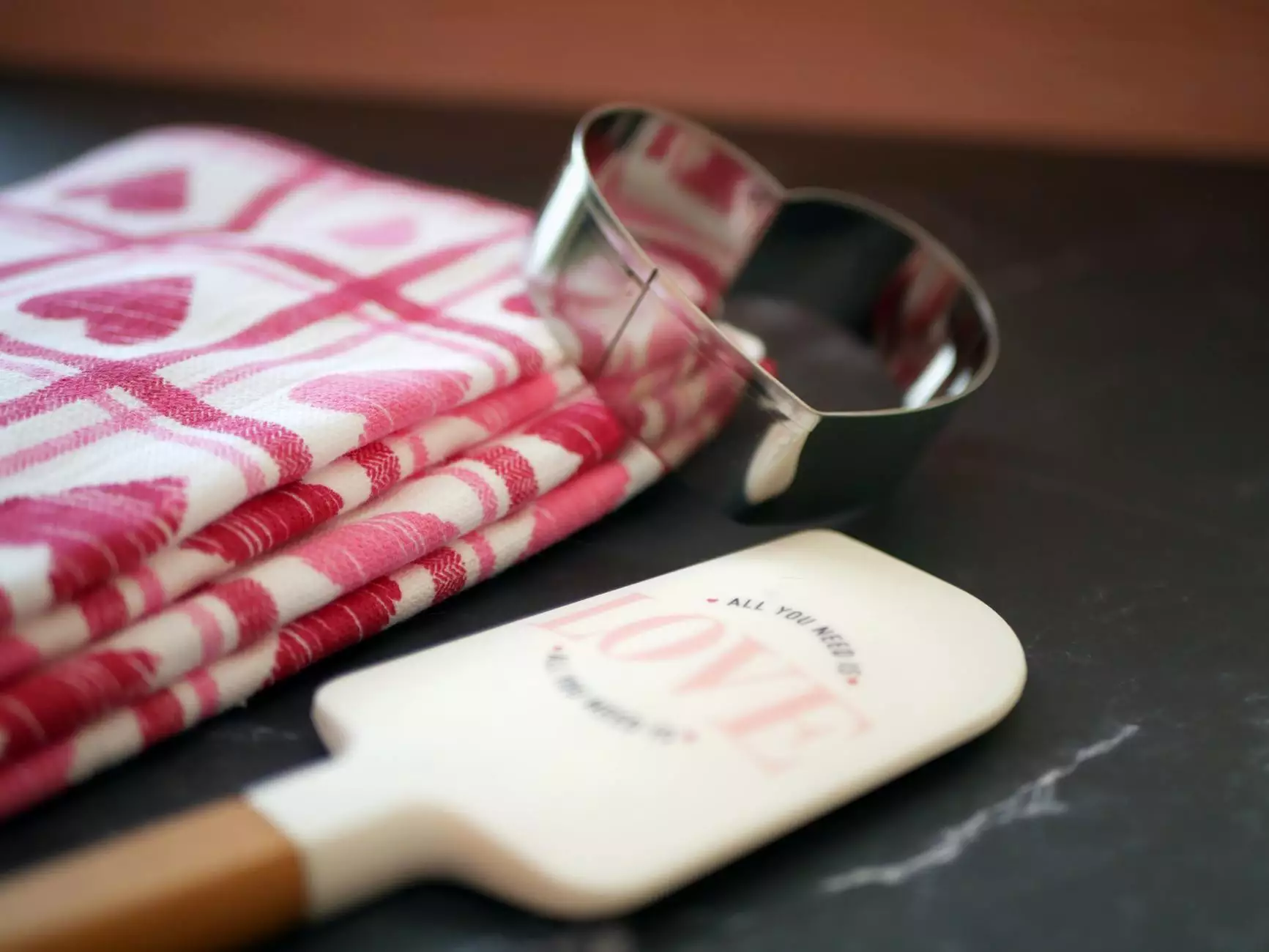
The automotive industry is constantly evolving, and one of the key technologies driving its transformation is injection molding automotive components. This manufacturing process allows for the creation of complex parts with precision, efficiency, and cost-effectiveness. In this article, we will explore the intricacies of injection molding and its significant impact on automotive manufacturing.
Understanding Injection Molding
Injection molding is a manufacturing process used for producing parts by injecting molten material into a mold. This process is incredibly versatile and can be used with various materials, including plastics, metals, and composites. The method is particularly popular in the automotive sector due to its ability to produce high volumes of identical parts consistently.
The Process of Injection Molding
The injection molding process can be broken down into several key steps:
- Material Preparation: The selected material, often plastic for automotive parts, is fed into a hopper and heated until it reaches a molten state.
- Injection: The molten material is then injected into a closed mold at high pressure, allowing it to fill all cavities.
- Cooling: Once the mold is filled, the material is cooled, solidifying into the desired shape. This cooling phase is crucial for ensuring dimensional accuracy.
- Demolding: After cooling, the mold is opened, and the finished part is ejected. Additional finishing processes may occur at this stage.
Materials Used in Injection Molding for Automotive Parts
When it comes to injection molding automotive applications, the materials selected play a crucial role in the part's performance. Common materials include:
- Polypropylene: Known for its chemical resistance and toughness, it is frequently used for interior and exterior automotive parts.
- Acrylonitrile Butadiene Styrene (ABS): This material provides excellent impact resistance and is commonly found in automotive dashboards and components.
- Polycarbonate: Used for applications requiring transparency and high impact resistance, such as headlights.
- Thermoplastic Elastomers (TPE): These materials combine flexibility with durability, making them ideal for gaskets and seals.
The Advantages of Injection Molding in the Automotive Industry
Injection molding has emerged as a preferred manufacturing method in the automotive sector due to several compelling advantages:
1. Cost Efficiency
Injection molding allows for mass production of parts, significantly reducing the per-unit cost. Once the initial mold is created—often a substantial investment—producing additional parts becomes increasingly economical.
2. Precision and Quality
The precision of injection molding ensures that each part produced is highly uniform, reducing the need for secondary finishing processes. This level of accuracy is vital in automotive manufacturing, where even minor defects can lead to significant operational issues.
3. Design Flexibility
Injection molding supports a wide range of designs, enabling engineers to create complex shapes that enhance functionality and aesthetics. This adaptability is essential as automotive designs continue to evolve.
4. Reduced Waste
Traditional manufacturing processes often lead to significant material waste. Conversely, injection molding is highly efficient, using only the necessary amount of material to create each part, thus minimizing environmental impact.
Applications of Injection Molding in the Automotive Sector
Inject molding is utilized in various automotive applications, showcasing its versatility:
Interior Components
From dashboard panels to door handles, many interior components are manufactured using injection molding. The ability to produce intricate designs and textures enhances the overall aesthetic appeal of vehicles.
Exterior Components
Injection molding is also used to create exterior parts such as bumpers, fenders, and grilles. These components require materials that can withstand harsh environmental conditions while maintaining durability and style.
Functional Parts
Many functional automotive parts, such as clips, connectors, and housings for electronic components, are produced via injection molding. These parts often have precise specifications and must meet stringent performance standards.
Challenges in Injection Molding Automotive Components
While injection molding offers numerous benefits, it does not come without challenges:
1. Tooling Costs
The manufacturing of molds is a significant upfront expense. For low-volume runs, the cost of tooling may outweigh the benefits of using injection molding.
2. Material Limitations
Not all materials are suitable for injection molding. Some specialized materials may not flow well in molten form or may require specific processing conditions.
3. Process Complexity
Injection molding requires careful control over various parameters, such as temperature, pressure, and cooling time. Variations in these factors can lead to defects in the final product.
The Future of Injection Molding in Automotive Manufacturing
The future of injection molding automotive seems bright as the technology continues to evolve. Advancements in materials science, machine technology, and digital manufacturing processes are paving the way for innovations, including:
1. Sustainable Materials
With increasing pressure to reduce environmental impacts, the development of biodegradable and recycled materials for injection molding is becoming a focus area. This shift can significantly enhance the sustainability of automotive manufacturing.
2. Smart Manufacturing
The integration of Industry 4.0 concepts into injection molding processes, such as real-time monitoring and control systems, is improving efficiency and reducing error rates. The adoption of predictive maintenance will also ensure that machinery operates optimally, reducing downtime.
3. Lightweight Components
As the automotive industry moves towards electric vehicles, there is a growing need for lightweight components that improve energy efficiency. Injection molding can play a crucial role in creating these advanced, lightweight materials.
Conclusion
In conclusion, injection molding automotive manufacturing is a cornerstone of modern automotive production. Its ability to create complex, high-precision components at scale offers unprecedented advantages. As the industry continues to innovate with sustainable practices and advanced materials, injection molding will undoubtedly remain integral to the evolution of automotive technology. Companies like Deep Mould are leading the way in utilizing these advanced processes to ensure quality and efficiency in automotive manufacturing.